.
Wet fractionation is a process in which a raw material is separated into the many components that form the whole, original material. Materials are processed in the presence of a solvent (water, ethanol, etc.). Processing technologies associated with wet fractionation include, but are not limited to, wet milling, distillation and centrifugation.
(Click on the image to enlarge the equipment photo.)
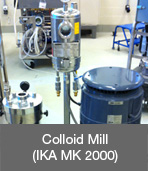 | Colloid Mill (IKA MK 2000)
- Materials can also be size reduced via a Colloid mill.
- The material is processed in solution and yields a fine particle slurry. This is useful to minimize molecular damage and combines a size reduction technique with a separation step.
- The colloid mill can also perform high-speed mixing of two different materials, such as protein and starch, in a solution. This will create micro-droplets or an emulsion. The finer the droplet, the more stable the final solution.
- Solutions can be separated into dry and wet fractions using a vibratory sieve or centrifugation technology.
- The vibratory sieve can be setup with 5 different screen sizes to separate particle based on size while removing free water (solvent).
- Depending on solids content a decanting or disc centrifuge can also be used to separate solids from solvent.
- The decanting centrifuge is used to process solutions with a solid content between 15% and 40% and the continuous (disc) centrifuge will process solutions with a solid content of 3% to 15%.
- There is also a Solvent-compatible centrifuge that is safe to use solvents like ethanol, hexane, and methanol.
- Solutions can also be dried to a powder using spray drying technology.
- The solution is pumped into a very hot chamber, and water is immediately evaporated to yield a fine powder.
- Spray drying offers a very flexible control over powder particle properties such as density, size, flow characteristics and moisture content.
- Primarily projects have centered on starch and protein separation. There has also been work done in the areas of plant extracts and pulp waste separation.
|
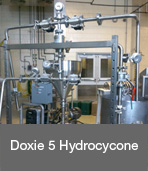 | Doxie 5 Hydrocyclone
- Maximum working pressure: 150 psi
- Uses: removal of particle in the 3-8 microns in diameter from liquid stream.
- Capacity: 1 GPM
|
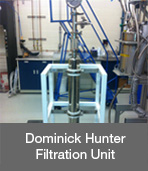 | Domnick Hunter Filtration Unit
- Model: VSHCE-013-BTB-T-S
- cartridge: 1 30" filter
- Material: stainless steel
|
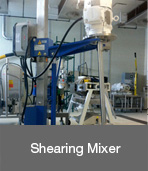 | Shearing Mixer
- MSM ® type 100 shear mixer drive
- Motor power: 5 hp
- Motor speed: 3600 RPM
- Length: 31.5” (~800 mm)
- Working capacity: 550 L
|
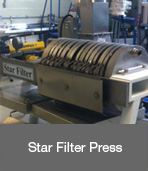 | Star Filter Press
- Model: 20-12A
- Working pressure: 0-40 psi
|
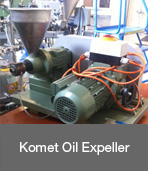 | Komet Oil Expeller
- Processing rate: 4-6 kg/hr cleaned rape seed with a moisture of between 6.5%-8.5% @ 16°C
|
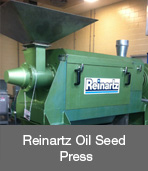 | Reinartz Oil Seed Press
- Type: AP 12
- Processing rate: 200kg/hr cleaned rape seed with a moisture of between 6.5 % - 8.5 % @ 16’C
|
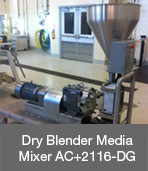 | Dry Powder Mixer
- Dry-Blender Media Mixer AC+2116-DG
- 316L stainless steel blender section
- 2” T/C powder addition port, 1.5” T/C liquid inlet/outlet ports
- Blender impeller: 5.75” diameter
- Drive motor: 5 Hp, 3500 rpm
- 304 stainless steel base plate – with feet
- Dimensions: 28.1” H x 22.8 W
|
| | 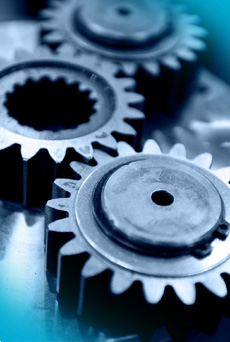
Alberta Agriculture & Forestry
Bio-Industrial Opportunities Section
O.S. Longman Building
4th Floor, 6909 - 116 Street
Edmonton Alberta T6H 4P2
Phone: (780) 644-8118
Email: biobranch@gov.ab.ca
Bio Processing Innovation Centre - Grand Opening and Open House
September 21, 2017
1:00 - 3:30pm
5520 - 36 Street, Edmonton, AB
Click here to register. |