| Direct seeding | Soil disturbance (of direct planting machines) | No-till (zero tillage) | Residue management | Residue clearance (through planting equipment) | Critical dimension | Direct planting equipment | Single and double shoot systems | Seed row spacing | Seed row width
Direct seeding is a relatively new approach to crop production and it uses some new terms. Not everyone uses these terms in the same way. The following definitions are those used in this Direct Seeding series.
Direct Seeding
Direct seeding, like no-till, is a cropping system which aims to improve soil and soil moisture conservation. Direct seeding is more flexible than no-till; it allows some tillage to solve immediate weed problems and to deal with high moisture and heavy clay soil conditions.
In direct seeding, soil is not tilled in the spring before planting. This is to conserve soil moisture in the seedbed. Any fall tillage must leave the soil surface compact and level to preserve soil moisture. Most of the crop residue remains on the surface with at least half the stubble remaining upright and anchored to trap as much snow as possible. Typical operations are fall fertilizer banding with knives, and redistributing crop residue and incorporating herbicides with heavy or rotary harrows.
The amount of soil disturbance during direct planting varies with the type of opener.
Soil Disturbance (of Direct Planting Machines)
With low soil disturbance direct planters, less than 40 per cent of the original soil surface is physically worked up by the openers to form the furrow for seed placement. Some soil from the opener's action may be deposited between furrows, giving the appearance of more soil disturbance. Low soil disturbance can be expected from a 75-mm (3-inch) wide opener spaced at 225 mm to 300 mm (9 to 12 inches) between opener centres. Soil firmness, moisture conditions and planter speed may affect the amount of soil disturbance. Low disturbance direct seeding systems are very much like no-till systems except that some tillage options remain available in direct seeding.
High soil disturbance direct planters disturb more than 40 per cent of the soil surface. If fall tillage was done, then planting is into loosened soil and results in most of the surface being disturbed. Ground openers wide enough to overlap will disturb the entire soil surface to some degree. Sweep openers produce high disturbance. They give varying degrees of weed control, so a pre-seeding herbicide application may not be needed. However, they may also create a seedbed for weed seeds and volunteer seeds from the previous crop. High disturbance openers may require additional seedbed finishing to cover the seed and to improve weed control.
No-till (Zero Tillage)
In a no-till cropping system, planting is the only operation which disturbs the soil. Only 25 to 35 per cent of the soil surface is disturbed. Most openers require that much disturbance to place the seed and fertilizer into a seedbed. Many farmers, however, strive for less than 25 per cent disturbance. No-till is similar to low disturbance direct seeding except that direct seeding systems allow some tillage to deal with unusual conditions.
No-till aims to minimize soil disturbance and maintain as much crop residue cover as possible because:
- low disturbance reduces soil moisture loss.
- weed seeds are less likely to germinate and grow on the undisturbed soil surface.
- low disturbance systems use less fuel for field operations.
- crop residue cover protects soil from wind and water erosion.
- standing stubble traps snow.
Residue Management
This term is used to refer to:
- the process of assessing field conditions (during and after harvest) and considering seed and fertilizer placement, in order to make informed decisions about machine selection and field methods to manage crop residue.
- the use of machinery and methods to prevent crop residue from interfering with successful crop production.
In direct seeding systems, residue management begins at harvest. See Residue Management for Successful Direct Seeding (Agdex 570-4) and Handling Difficult Crop Residue Conditions (Agdex 519-2) for more information.
Residue Clearance (Through Planting Equipment)
Residue clearance is the ability of planting equipment to allow crop residue to pass through without bunching. Ground openers and shanks are shaped to prevent dragging and subsequent bunching of straw residue. The opener must prevent chaff residue from falling into the seed furrow and causing poor seed cover and poor furrow closing.
Critical Dimension
This is the distance between two points in a machine where plugging with straw is likely to occur. The most common locations for plugging in the planter are:
- between the underside of the shank (may be the spring trip supporting mechanism) and the soil surface.
- between one ground opener and the next.
- between a ground opener and a wheel or some other adjacent structural member.
The effect of critical dimension may vary with the amount of crop residue on the surface, the moisture content of the residue, or even the air conditions at the time. Damp straw plugs quite easily. Fluffed up straw plugs more easily than straw lying on the soil surface. Dry straw on a warm, breezy day will pass through a planter whereas damp straw may not. Changing speed and direction of travel may help a planter to clear crop residue.
The straw handling performance of many planters may be improved by modifying the location where plugging most often occurs. That location may need the spacing increased, sometimes greatly, to prevent plugging.
Direct Planting Equipment
Air seeder
An air seeder is a planter which uses a medium or heavy duty cultivator, a central pneumatic seed and fertilizer delivery system, and a ground opener for seed and/or fertilizer placement. This system offers many options and adaptations to meet a variety of conditions. The planter's main frame is carried on and controlled by wheels inside the frame. The attitude (fore - aft) levelling is controlled by caster wheels in front of the frame (floating hitch type). This method of depth control is superior on land with sharp hills or gullies. When the ground opener type is chosen, the appropriate seed row finishing equipment must be installed on the rear of the air seeder. Separate soil finishing passes must be made over the planted field to ensure good seed placement depth.
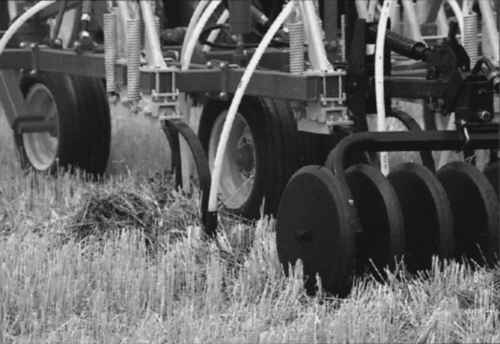
Figure 1. Air Seeder.
Air drill
An air drill is an adaptation of the air seeder. The main difference is that air drills do not have wheels inside the frame carrying the ground opener hardware. The support for the machine and its depth control comes from the dedicated packer wheels on the rear of the drill. The front is carried and controlled by forward caster wheels as with any floating hitch cultivator.
An air drill has all the advantages of an air seeder, such as good seed depth control, wing-up convenience for transport, a central seed and fertilizer metering system, and excellent field efficiency and capacity. It also has two main advantages over an air seeder: the relatively constant packing force delivered by each on-row packer, and the increased residue clearance made possible by the absence of inside-the-frame wheels.
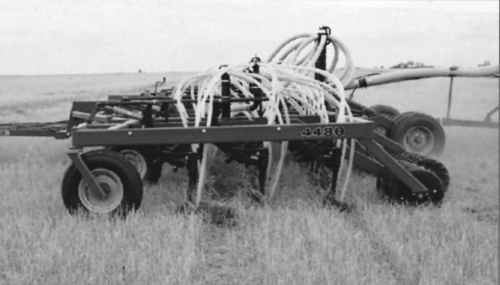
Figure 2. Air drill.
Ground opener
This is the soil engaging part of a planter. It is responsible for placement of seed and fertilizer. It has a soil-breaking wear point, a soil dividing body, and delivery tubes to guide seed and fertilizer to the furrow bottom. Also, it often has deflecting surfaces to guide soil back around the fertilizer bands and seed rows.
A ground opener must:
- create distinct rows or bands of seed and fertilizer.
- leave at least 15 mm (0.6 inches) of soil between the fertilizer bands and seed rows.
- not place seeds in the fertilizer band.
- create a good soil structure (fine aggregates) in the seed zone.
- have low draft requirements.
- resist wear. (Resistance performance is measured in terms of how many acres each opener plants. For example, if 40 openers on one machine plant 4000 acres, then each opener plants 100 acres.)
- scour well in moist and high clay content soils. (Many openers tend to build up with soil, causing the furrow opening to be too large. As a result, the seed is generally not covered with sufficient soil.)
- leave the soil surface smooth enough for subsequent operations like crop spraying and harvesting.
- sufficiently "blacken" the soil surface in the seed row if there is a concern about soil being warm enough for seed germination.
Single and Double Shoot Systems
The terms "single shoot" and "double shoot" refer to how material (seed and fertilizer) is delivered by the planter to the ground opener.
A single shoot system has only one delivery line going to the ground opener. The line carries seed and possibly some granular fertilizer.
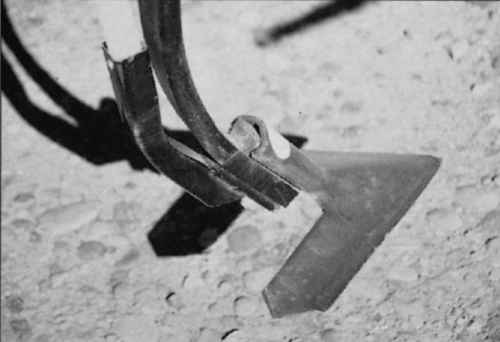
Figure 3. Single shoot opener.
A double shoot system has two lines going to the ground opener. These may be two air flow lines or an air flow line and a liquid fertilizer or anhydrous ammonia (NH3) line.
Most often, a double shoot system has a ground opener which opens two separate furrows so the seed is placed in one furrow and the fertilizer in the other. This type of fertilizer placement is called side banding. The fertilizer band is placed deeper than the seed, usually about 25 mm (1 inch). Seed is placed either in one row, above and to the side of the fertilizer band, called double shoot single side banding (Figure 7c), or in two rows above and on both sides of the fertilizer band, called paired row double shooting (Figure 7b).
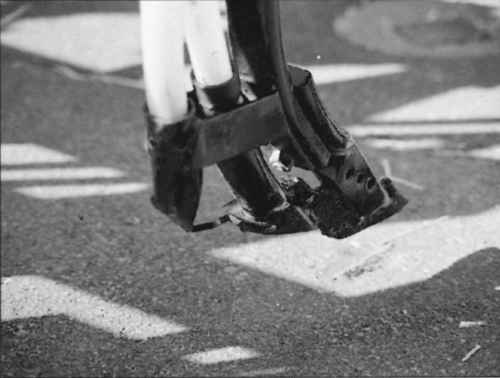
Figure 4. Double shoot single side band opener.
Double shoot systems are sometimes set up so both lines come together at the opener to place the seed and fertilizer in the same furrow. This setup is sometimes called single furrow double shooting. It is used when the best option for existing soil conditions is to place the fertilizer in the seed row. This setup offers an advantage over a single shoot system because it allows the fertilizer rate to be changed on-the-go, while the seeding rate stays the same. The ground opener is similar to that used for a single shoot system except that the two lines are combined with a "Y" adapter or an attachment is used to position the two lines into the seed bed.
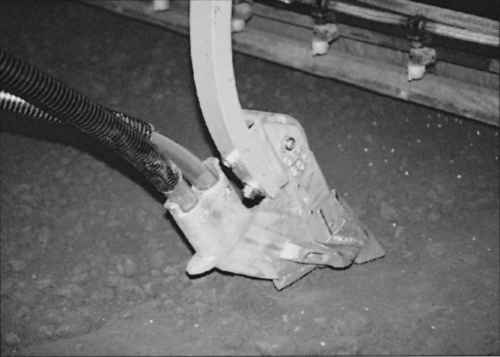
Figure 5. Double shoot paired row opener.
A semi-dependent opener is a variation on the double shoot single side band opener. It forms distinct furrows and leaves a seed row slightly narrower than the opener. The seed opener follows behind and slightly to the side of the fertilizer point, ensuring that soil covers the fertilizer band before the seed is placed. There is little chance of fertilizer and seed mixing.
For more information on openers, refer to Ground Opener Systems (Agdex 519-24).
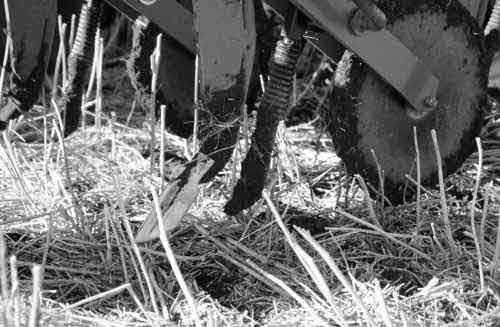
Figure 6. Semi-dependent opener.
Seed Row Spacing
This is the distance from the centre line of each individual seed tube outlet to the centre line of the adjacent seed outlet (Figures 7a, 7b, 7c). Each ground opener may have one or two seed outlets.
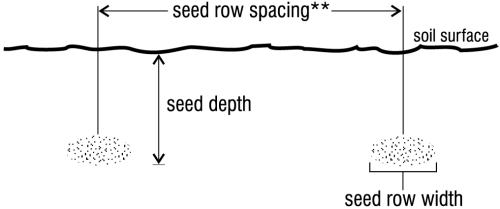
Figure 7a. Seed rows from single shoot openers*.
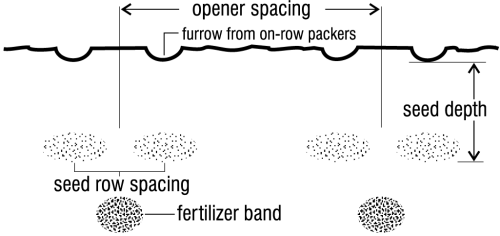
Figure 7b. Seed rows from double shoot paired rwo openers*.
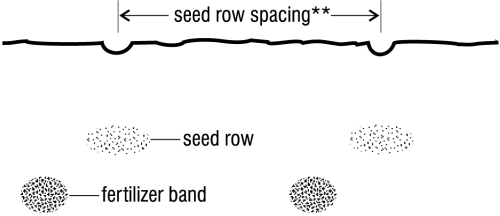
Figure 7c. Seed rows from double shoot single side band openers.
* On-row packers create furrows above the seed row. Single shoot systems may not have on-row packers.
** Seed row spacing is the same as opener spacing.
Uniform row spacing occurs when each opener has only one seed outlet. It can also occur when each opener has two seed outlets and the outlets are a distance apart equal to one half the opener spacing.
Paired rows usually refer to the situation where the two seed outlets on an opener are less than half the opener spacing apart. For example, several double shoot openers have seed outlets spaced 75 mm (3 inches) apart and ground openers spaced 250 mm (10 inches) apart (Figure 8). This is referred to as a three/seven paired row; that is, 3 inches between the centre of the paired rows and 7 inches to the centre of the first row of the next set of paired rows.
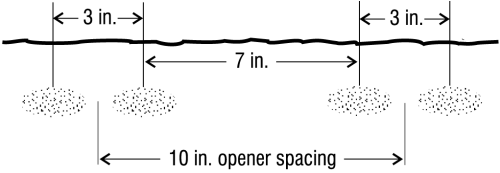
Figure 8. An example of paired row spacing - three/seven paired rows*
* The spacing between seed outlets and openers varies with the make of opener.
Seed Row Width
This is the width of the seed row created by each seed outlet. Some types of seed outlets spread seed in a broad row up to 200 mm (8 inches) wide, such as a wide deflector under the cultivator sweep of an air seeder. Other types spread seed in a very narrow row, such as the offset double disc of a no-till drill.
Seed row width is important in determining the amount of fertilizer that can be placed into the seed row. The seed row width as a percent of the total row width is called the seed bed utilization. This term is used by soil specialists to describe how fertilizer was applied, particularly with single shoot openers.
Prepared by:
Murray Green, Engineering Services Branch, Alberta Agriculture and Food
Factsheets in the Direct Seeding Series are also available through Alberta Agriculture's Internet site.
Source: Agdex 570-7. Revised April 1999.
U10/04 |
|