| Structural design | Concrete specifications | Concrete finishing | Floor drains | Summary
In designing floors for the milkhouse, both structural and functional requirements must be met. The structural design refers to the ability of the floor to (usually) carry the heavy load of bulk tanks, and to otherwise be free from cracks and settlement. No floor movement can be tolerated as this will affect bulk tank calibration.
Functional design mean floors that are durable, easy to clean and a reasonable cost to construct. Proper slope and good floor drains are important functional components. Often there is a relatively small added cost if the highest quality concrete and construction methods are used.
Floor movement caused by frost penetration along the foundation is a common problem which will not occur if the foundation is insulated and the building heated. Foundations should be insulated on the outside (see Figure 3) to prevent frost problems most effectively. This technique can also be used to insulate existing buildings which have experienced frost and ice on the foundation.
Table 1. Typical design data for bulk tanks
TANK SIZE | WEIGHT ON ONE
LEG OF TANK* |
Litres or kg (US gal) | kg (lb) |
1900 (500) | 600 (1350) |
3800 (1000) | 1150 (2500) |
7500 (2000) | 2200 (5000) |
11,500 (3000) | ** (**) |
* Weight per leg is total weight divided by 4; this includes an estimate for the weight of the tank.
** Large tanks, with more than 4 legs may not have the load equally distributed. For example with 6 legs, half the load may be on the centre pair of supports.
Structural Design
Bulk tanks exert heavy concentrated loads on the floor at support points. There are a variety of ways to accommodate these loads (Figure 1), the most practical being a structural slab (a) or grade beam footings (b).
The structural slab is usually most practical, because it allows a variety of bulk tank sizes to be used, and the reinforcing for structural support will be more than adequate to prevent floor cracking from other causes.
Very large bulk tanks, particularly tanks that are bulk-headed so as to be partially outside the milkhouse, may require heavy grade beams and footings. Figure 2 illustrates a grade beam foundation for this application. Grade beams like this may result in a small saving in materials. Because these supports must be under the legs of the tank, they may not be as adaptable to changing the size of bulk tanks.
Subgrade preparation is the single most important part of a good quality floor slab. If the subgrade is uneven, or contains voids or soft spots, no concrete slab will perform well, regardless of reinforcement. The subgrade should consist of a thick, compacted granular base of gravel or crushed stone. All topsoil, and any other loose soil, should be removed.
Structural slabs are relatively thick concrete floors (150-200 mm) (6"-8") with sufficient reinforcing to handle the stress of heavy loads. Reinforcing is required for concentrated loads, and to prevent shrinkage and stress cracks that occur during curing. Though the structural design of slabs for point loads is complex, the practical results boil down to the values in Table 2. Figure 3 illustrates the main design requirements.
Floor thickness of 150 mm (6") is adequate for most applications, with appropriate reinforcing. Reinforcing rods need be located only under the bulk tank area. In practice, however, about half the steel is carried on out to the edge of the floor, with the main steel spread over the area of the bulk tank. Very large tanks may require thicker floor slabs.
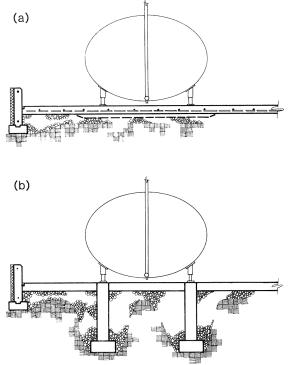
Figure 1:
Foundation systems for bulk tanks; |
(a) | reinforced concrete floor slab, |
(b) | independent grade beam and footings. |
Shallow piles (figure 4) are not recommended. Consisting essentially of 200 mm (8") post holes filled with concrete, these will not effectively carry large loads. A pile designed for a 2000 kg (4400lb) load would have to be at least 300 mm (12") diameter by over 5 m (16 ft) deep. A shallow pile can be used if it has a wide footing under it. The piles must be located under the tank legs, which does not readily accommodate changing the bulk tank.
Concrete Specifications
Durability, which is resistance to chemical attack, is the most important quality of a concrete floor. The fatty acids in milk and strong cleaning detergents are extremely corrosive to concrete. Premature failure of floor surfaces is a common problem with milkhouse and parlor floors.
Note too, that these same high quality concrete techniques are the key to performance of milking parlor and feed manger floors - the other areas in a dairy which are subject to concrete deterioration.
The following specifications are required to obtain high quality, durable concrete:
- high strength concrete 35 MPa, (5000 PSI), minimum
- a low slump, low water content mix
- specify 5 per cent air entrained concrete
- proper finishing
- moist curing
- consider using a curing and sealing compound
- place with a vibrator
Concrete strength is the single most important factor in concrete durability. Concrete of 35 MPa (5000 PSI) compressive strength is about 10 times more durable than 20 MPa (3000 PSI) concrete, normally used for foundations and sidewalks. Air entraining also makes concrete much more durable.
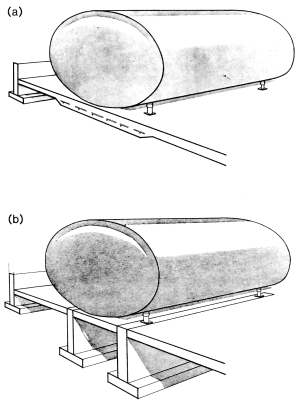
Figure 2:
Foundations for very large tanks 11 500 L (3000 gal) and larger: |
(a) | thick reinforced slab:
reinforcing - 15M rods at 300 mm (12")
0. C.
thickness - 200 to 250 mm (8 to 10"). |
(b) | grade beams on spread footings 500 to 800 mm
(20 to 32") wide, this support is required for bulk-headed
tanks (floor may also cover the grade beam). |
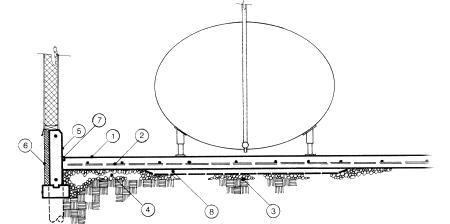
Figure 3:
Milkhouse floor reinforced to support a bulk tank.
1. 150 mm (6") concrete floor (typical).
2. Reinforcing steel (see table 2); half this amount may be used 600 mm (2') away from the bulk tank.
3. Uniform subgrade.
4. Compacted granular base.
5. Foundation on footings or grade beam on piles.
6. 38 or 50 mm (1 1/2" - 2") rigid foam insulation with protective covering.
7. 5 mm joint, caulk with flexible, waterproof sealant.
8. Floor may be thicker under heavier tanks.
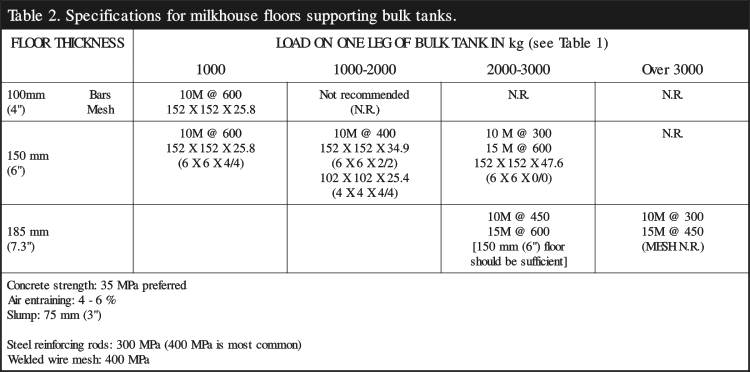
Reinforcing shown as standard metric bar size and spacing (mm), or welded wire mesh metric (Imperial) designation.
Concrete Finishing
Proper finishing has a great effect on surface durability. Aluminum or magnesium float finish, followed by steel trowelling gives the best results. The most important aspect of trowelling is to not work the surface until the concrete has taken initial set and the water sheen has disappeared. The surface should then support "knee boards" for trowelling.
Steel trowelling makes the surface dense and durable. Smooth concrete can be slippery when wet. (There is always a compromise between "easiest to clean" and a less slippery surface). Light brushing with a broom after trowelling improves the traction. Commercial slip-resistant surface treatments can also be used.
Damp curing of concrete, for at least five days, is essential for high durability. Poorly cured concrete may be internally up to strength, but the vital surface layer will not be strong and durable. Damp curing can be achieved by covering with a vapor barrier, wet burlap or tarpaulin; or by applying a curing compound after the concrete has set. Proper curing and high strength make for good quality concrete. Additional concrete durability can be achieved by applying a surface hardener and sealing compound. Various commercial products are available, which, in general, perform similar functions. These are of two types:
(1) liquid emulsions applied to the surface several days after it is finished, and
(2) dry-shake powders which are applied and trowelled into the surface of fresh concrete at the last trowelling operation. Both are satisfactory.
Be sure to follow manufacturers' directions closely to obtain best results from this treatment.
Concrete mortar, used to grout around tank legs, may not adhere well to concrete floors which have had a surface hardener treatment. Special concrete grout is available that will do the job.
Floor Drains
Floors should slope at about 1 per cent towards floor drains, with a faster slope the last 4OO mm (16"). Good floor drains are an integral component of the sanitizing system. All drains must be properly trapped.
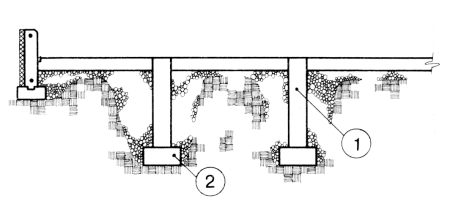
Figure 4:
Shallow piles (1.) are not effective at carrying large loads unless a footing (2.) is placed under the pile or the pile is about 400 mm (16") in diameter by 5 - 8 m (15 - 25 ft.) deep.
Two floor drains are usually required, one under the wash vats, the other near the bulk tank outlet. This drain is required to be no closer than 400 mm (16") to the tank outlet, and cannot be under the tank.
Summary
A quality concrete floor will provide a lifetime of trouble-free service. Using high strength concrete and proper design and finishing techniques should yield the desirable results.
Prepared by:
Dennis Darby, P. Eng.
Farm Structures Engineer
Source: Agdex721-7. |
|