| Residue management methods | Harvest | Post-harvest | Seeding | Key points
Crop residue management is essential for successful direct seeding. Maintaining crop residue, rather than baling, burning or tilling, offers many benefits. These include increased snow catch and water infiltration, reduced moisture evaporation, increased soil organic matter, improved soil structure and plant nutrient cycling, virtually no chance for wind erosion and much reduced potential for water erosion, and the reduction of some weed species.
Crop residue must be spread evenly to avoid or reduce such problems as: equipment plugging; poor seed germination; disease, weed and insect infestations; nitrogen tie-up in the chaff or straw rows; and cold soil.
Residue Management Methods
The goal of residue management is to make the conditions adequate for the ground opener to perform its primary function of seed placement. This means the residue must flow smoothly around the opener with no plugging, bunching or lumps of crop residue piling on the seed row (Figure 1). In the Brown and Dark Brown soil zones, stubble is kept standing for snow trapping and wind erosion control. In the Black and Gray soil zones, the main concerns are handling large volumes of crop residue and ensuring soils drain and warm sufficiently in the spring.
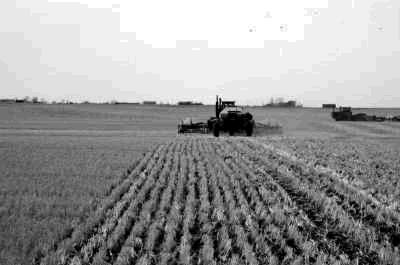
Figure 1. Uniform planting in standing stubble
Residue management economics vary from farm to farm, depending on the equipment used and the amount of residue. Adding chaff and straw spreading attachments to the combine is well worth the cost. The investment is always paid off through better crop emergence and machinery field efficiency.
Harvest
Combining
The most practical way to manage crop residue is with the combine. The residue should be spread uniformly over the entire width of the header cut.
You may need to purchase spreading attachments for your combine to achieve uniform residue distribution. These systems use varying amounts of horsepower to operate, so they affect costs as well as combine performance and capacity. A number of adjustments can be made to most new chopper/spreaders so the spread will match the header width under the crop conditions at the time.
Using a wide cutter header or a double swath makes uniform spreading more difficult, and after-market or modified straw and chaff spreading attachments may be required.
Chaff spreading
Chaff spreading must occur at harvest. Harrowing or tillage equipment is not effective in spreading chaff.
Two types of chaff spreading systems are available. One type uses one chopper/spreader for the straw and a separate spreader under the combine shoe for the chaff. The other type mixes the chaff with the straw which ensures good spread of the chaff.
Stubble height
Cereal stubble height should generally not exceed the seed row spacing, at least until some experience is gained in different crop conditions on the farm. Taller stubble may cause plugging of tine-type seeding equipment. Seeders equipped with cutting disc coulters or angled disc openers, however, do not plug in the taller stubble.
Post-Harvest
Harrowing
Harrowing may be needed to achieve uniform residue distribution, especially for heavy crop residues. Harrows can spread straw but not chaff. It is better to harrow in the fall before the straw has settled. Increasing harrowing speed increases the spreading action, but also increases the risk of knocking down standing stubble.
Tine harrows will often satisfactorily spread straw. They depend on dry straw conditions to do a uniform job. Adjustments to give a smooth flow of straw are not easy with older models. Heavy harrows are better at spreading straw after harvest or breaking up surface straw in the spring. Many models can be adjusted from the tractor to match field conditions at that moment. Some have down pressure features to increase the action and control bounce of the harrow frame. Heavy harrows can also satisfy the incorporation requirements of some herbicides. Travel speed is between 10 and 15 km/hour. Power requirements are usually 200 hp and up.
Oscillating harrows, although no longer common, often provide the best action for spreading evenly settled straw, but warm, dry conditions are important for efficient equipment operation. The aggressive action of these harrows makes shallow incorporation of granular herbicides possible. Travel speed is limited to 4 to 5 miles/hour (6 to 8 km/hour).
Rotary harrows are ideal for shallow incorporation of herbicides into the soil. These harrows rarely plug up and they leave the residue on the soil surface. However, they do not spread straw. Take care not to harrow too much because the loose straw left on the surface may be blown away by strong winds.
Mowers and shredders
Mowers and shredders are available in two basic types: rotary or flail. Power requirements for both are relatively high, but they produce a more uniform residue cover. A balance is needed between standing stubble and chopped residue on the surface. Too much chopping to create short or no stubble leaves a matt of residue which may not flow around the ground opener.
Seeding
Planting equipment
Increased residue clearance of seeding equipment is crucial. This can be achieved by: increasing the row spacing, increasing the distance between openers, or increasing the number of ranks of openers. Adequate depth from ground level to the bottom of the seeder's frame is also very important. The type of seeding implement you choose must match your crop residue conditions.
Crop type and variety
You can increase or decrease the amount of crop residue produced by choosing a different crop type or variety. In cereal crops, for example, a semi-dwarf variety can reduce the amount of crop residue produced per bushel of grain by up to 25 per cent. Also see Estimating the Value of Crop Residues (Agdex 519-25) and PFRA's Managing Crop Residues on the Prairies: Crop Residue Survey.
Key Points
- Crop residue management is essential for successful direct seeding.
- The most practical way to manage crop residue is with the combine.
- The residue should be spread uniformly over the entire width of the header cut.
- Chaff spreading must occur with the combine.
- Stubble height should generally not exceed the row spacing, until some experience is gained in different crop conditions on the farm.
- Harrowing can spread straw but not chaff. It is better to harrow in the fall before the straw settles.
- Mowers and shredders have high power requirements, but they produce a more uniform residue cover and can correct a residue problem.
- Seeding equipment must have increased residue clearance.
- Crop type and variety influence the amount of crop residue.
More information on residue management is available in Handling Difficult Crop Residue Conditions (Agdex 519-2) and Equipment Issues in Crop Residue Management (Agdex 519-4).
Prepared by:
Murray Green, Engineering Services, Alberta Agriculture, Food and Rural Development, and Don Poisson.
Source: Agdex 570-4. Revised July 1999 |
|