| Anaerobic digestion | Ethanol production | Confined feeding operations (CFOs) | Rationale for the integrated system
Alberta has many agricultural operations, and all of them generate various types of organic wastes. These organic wastes require proper handling to reduce pollution and contamination. Using anaerobic digesters to process these organic wastes appears to be an attractive option since the anaerobic digestion process can stabilize biologically active organic wastes and produce biogas.
Biogas may also be called renewable natural gas because biogas can be used as a fuel source to produce electricity and heat like natural gas. Given the number of clusters of agricultural operations in Alberta, there may be a potential to integrate biogas plants with other operations.
This factsheet explores an integrated system consisting of an ethanol manufacturing facility, a confined feedlot operation (CFO) and a biogas plant. It is well known that the demand for ethanol-blended fuels is growing since replacing fossil fuel usage with renewable fuel remains a top environmental challenge.
At least one integrated system similar to the above-mentioned concept has been built in North America in the recent past. Therefore, the following sections briefly describe these integrated systems with flow diagrams including the energy requirement (biogas volume) and a hypothetical example calculation.
Anaerobic Digestion
Anaerobic digestion is a naturally occurring process through which organic matter such as manure, feed spills, meat processing wastes and crop residues are stabilized by micro-organisms strictly in the absence of air. During this process, some organic compounds are converted to methane (CH4) and carbon dioxide (CO2) gases. This mixture of gases is known as biogas. The composition of biogas is 50 to 75 per cent CH4 and 25 to 45 per cent CO2.
Like natural gas, biogas can also be used as a fuel in power generators, engines, boilers and burners. In practice, specially designed and insulated tanks are used to facilitate the anaerobic digestion process under a controlled atmosphere. These tanks are known as anaerobic digesters.
The effluent coming out of the digester after the completion of this process is known as digestate. Digestate has nutrient value and can be applied to the land like manure. Digestate also has much less odour compared to stored manure.
Ethanol Production
In North America, most commercial ethanol is produced by fermenting starch containing grain such as wheat, barley and corn. However, wheat and triticale have the best potential for producing ethanol in Alberta. A mass flow diagram of this process is shown in Figure 1. Since wheat and triticale have almost the same ethanol yield, their production requirements are assumed to be the same in this factsheet.
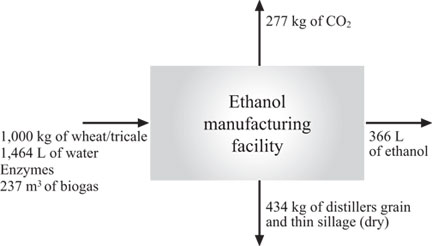
Figure 1. Ethanol production from wheat/triticale.
Actual ethanol production has three steps:
- feed preparation
- fermentation
- distillation
In the feed preparation step, the feedstock is subjected to grinding, the addition of water, heating and the addition of enzymes to hydrolyse the starch. The product that comes out of this step is known as mash.
The next step is fermentation. During the fermentation process, enzymes break down protein and starch into sugar and then yeasts, single celled living organisms that convert most of the sugar compounds into ethanol and CO2. The fermentation process releases a considerable amount of CO2. The fermented liquor containing alcohol is known as beer. Beer has an ethanol concentration of between 9 to 14 per cent.
As ethanol has a lower boiling point than beer, ethanol is separated using the distillation step. The separated ethanol mixture is 95 per cent ethanol and 5 per cent water. This 95 per cent ethanol is then dehydrated to 99.7 per cent ethanol and denatured by adding 2 to 5 per cent gasoline. The beer coming out after the distillation step is known as whole stillage or distiller’s grain.
Confined Feeding Operations (CFOs)
According to Statistics Canada and the Alberta Beef Producers, about 5.5 million cattle are on more than 20,000 Alberta beef cattle operations in 2014. This large number of CFOs produces a large quantity of manure, which is a cause for concern and often limits opportunities to expand an operation. Large CFOs are good candidates for integrated opportunities as they require a considerable quantity of grains and roughages, and distiller’s grain can replace some of this feed requirement.
Rationale for the Integrated System
Anaerobic digesters can process a large quantity of manure from CFOs and produce biogas, which is a renewable energy source. Ethanol plants are often located near agricultural operations as the feedstock for ethanol production is mostly from grains such as corn, wheat and barley. Energy intensive ethanol production could use biogas “renewable energy” to meet its energy demand if the ethanol and biogas plants were located close to each other.
Ethanol production produces a large amount of whole stillage as a by-product, which has dry matter to 12 to 14 per cent. Centrifuging the stillage can concentrate the solids to 30 to 35 per cent dry matter to produce wet distiller’s grain. These wet solids are a valuable source of protein for cattle and can replace at least 20 to 40 per cent of the cattle’s feed intake depending on the dietary nutrient requirements and cattle performance.
The remaining liquor after centrifuging is known as thin stillage. Thin stillage may have up to 7 per cent organic matter in the form of suspended and dissolved solids and can be fed to anaerobic digesters to enhance biogas production. The wet distiller grain has a shorter shelf life. Drying this material will be expensive. Alternatively, it may be fed to cattle in nearby feedlots without drying.
Ethanol blended with gasoline is sold as fuel for automobiles to reduce emissions and fossil fuel consumption. The ethanol manufacturing process also releases CO2, which can be trapped and sold to other industries. A schematic diagram of the components of a similar integrated system is shown in Figure 2.
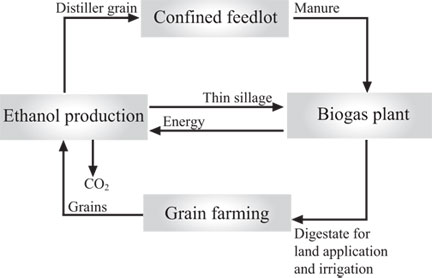
Figure 2. Schematic diagram of an integrated system consisting of an ethanol plant, CFO, grain farm and biogas plant.
The following equations are necessary in determining the feasibility of this integrated system.
Confined feeding operation
1 beef animal = |
 | 8.8 tonnes of manure (8 - 12 per cent solids)/year |
1 dairy animal = |
 | 22.6 tonnes of manure (12 per cent solids)/year |
Grain feed requirement for beef cattle = |
 | 0.90 tonne/animal/year |
Grain feed requirement for dairy cattle = |
 | 2.05 tonne/animal/year |
. |  |
Biogas plant |
1 tonne of beef manure (8 - 12 per cent solids) = |
 | 46 m3 of biogas + digestate for land application |
1 tonne of dairy manure (12 per cent solids) = |
 | 32 m3 of biogas + digestate for land application |
1 tonne thin stillage (7 percent organic content) = |
 | 48 m3 of biogas + digestate for land application |
1 m3 of biogas = |
 | 20 MJ or 1.7 kWh and 7.7 MJ when used as fuel in a co-generator |
Example calculation
Determining the quantity of wheat, energy and feedstock material for a biogas plant to produce 25 million litres of ethanol in a year:
a. Grain requirement
Ethanol yield from 1 tonne of wheat = 366 L of ethanol
Quantity of wheat required to produce 25 million litres of ethanol = 25,000,000/366
b. Biogas needed
Amount of biogas needed to process 68,306 tonne of wheat = 68,306 x 237 m3
c. Distiller grain produced
The amount of whole stillage produced = 68,306 x 0.43
d. Biogas potential of thin stillage
25 per cent of the whole stillage is thin stillage
The quantity of dry thin stillage = 29,372 x 0.25
Thin stillage may contain up to 7 per cent solids
Quantity of thin stillage liquor = 7,343/0.07
The biogas potential of the fermented thin stillage liquor is = 104,899 x 48
e. Size of the feedlot
The balance biogas quantity required from cattle manure is
= 16,188,525 - 5,035,129
= 11,153,396 m3
Size of the feedlot = 11,153,396/46/8.8
Note:
- Density of ethanol is 790 kg/m3.
- Up to 25 per cent of the total distiller’s grain (whole stillage) is thin stillage, and thin stillage usually has up to 7 per cent solids.
- 20 to 40 percent of the total cattle feed requirement may be replaced with the distiller’s grain.
- Plant material may be used to maximize the biogas production like the addition of thin stillage in the anaerobic digesters.
f. Cattle feed replacement and excess distiller’s grain for selling
Amount of distiller grain available as cattle feed
= 29,372 – 7,343
= 22,029 tonne
Beef grain requirement = 897 kg /beef
Grain feed requirement for 27,673 beef cattle
= 27,673 x 0.897
= 24,823 tonnes (dry)
Distiller grain can replace at least 20 per cent of the cattle grain feed = 24,823 x 0.2
The maximum excess amount of distiller grain for selling = 22,029 - 4,965
g. CO2 production
The amount of CO2 produced = 68,306 x 0.28
Summary
The requirement for large quantities of grains should not be underestimated. For example, 68,300 tonnes of wheat is needed to produce 25 million litres of ethanol. This wheat tonnage is approximately 1 per cent of the total wheat production in Alberta. Also, an ethanol production facility consumes significantly high levels of energy.
When using biogas as fuel, large amounts of biomass are required to produce a sufficient quantity of biogas. In one case, it was estimated that a feedlot with 28,000 cattle would provide sufficient biomass to provide enough energy for an ethanol facility that could produce 25 million litres of ethanol annually.
In addition, an ethanol manufacturing facility produces a large amount of distiller’s grain as by-product. Finding a market for the distiller’s grain would improve the economics of ethanol production. If not, handling the excess distiller’s grain could be expensive. However, integrated systems like this often have the advantage of using the by-product of one operation as the feedstock for another operation, which means these systems are more efficient and make better economic sense than stand-alone independent systems.
For additional information, check the following documents:
Anaerobic Digesters, 768-1
Anaerobic Digesters: Frequently Asked Questions, Agdex 768-2
Biogas Energy Potential in Alberta, Agdex 768-3
Biogas Distribution – Rural Utilities Division of Alberta Agriculture and Rural Development
Prepared by
Alberta Agriculture and Rural Development
Mahendran Navaratnasamy, Lawrence Papworth – Agriculture Stewardship Division
James Jones – Bio-Industrial Development
Source: Agdex 768-4. Revised November 2014 |
|